Specific Energy and Aqua Water Supply Corporation: S8 Well Case Study
The Customer
Aqua Water Supply Corporation, the second largest water supply corporation in Texas, delivers retail water to customers in the greater Austin-area. Aqua’s service area covers 953 square miles and water is supplied from twenty-nine production wells. Aqua is always looking to improve operational efficiencies by implementing innovative technologies and applying sound asset management practices. As an early adopter of technology, Aqua has established itself as a pioneer of efficiency in the water space.
The Problem
Aqua has large well pumps that are significant consumers of energy. Several of these wells have variable frequency drives that allow pumps to operate over a range of speeds in response to varying demands and aquifer levels. Aqua was looking for technology that would continually adjust well pump speeds to minimize energy consumption while still meeting volume demands. In addition to their desire to minimize energy consumed, Aqua wanted to identify a cost-effective way to increase production at the S8 Well site that would not require Aqua to drill a new secondary well.
The Solution
Aqua’s S8 well produces up to 1,800 gallons per minute (gpm) from the Carrizo-Wilcox aquifer. The well is powered by a 250 HP submersible motor with a variable frequency drive. Aqua selected Specific Energy to install Dynamic Pump Optimizer (DPO) at this well site to optimize pumping and improve production. After easy installation of the DPO edge device, energy consumption immediately dropped by 28%, while the well maintained production to meet demand. Specific Energy’s DPO delivered energy savings using a physics-based model looking at live sub-second sensor data, adjusting pump speed to achieve peak energy efficiency under varying system conditions. Data received from the DPO concluded that instead of running the pump 6 hours a day at full flow, the pump could run at half flow 13.1 hours and accomplish the same volume at an annual savings of 81 MWh (megawatt-hours) or $10,200/year.
Reducing Operating and Maintenance Costs
The DPO ensures that the well pump always operates within its “sweet spot”, or Preferred Operating Range (POR), minimizing impeller wear and reducing operation and maintenance (O&M) costs. By dynamically adjusting speed in response to varying system conditions, the pump always operates at peak energy efficiency, leading to reduced wear and tear.
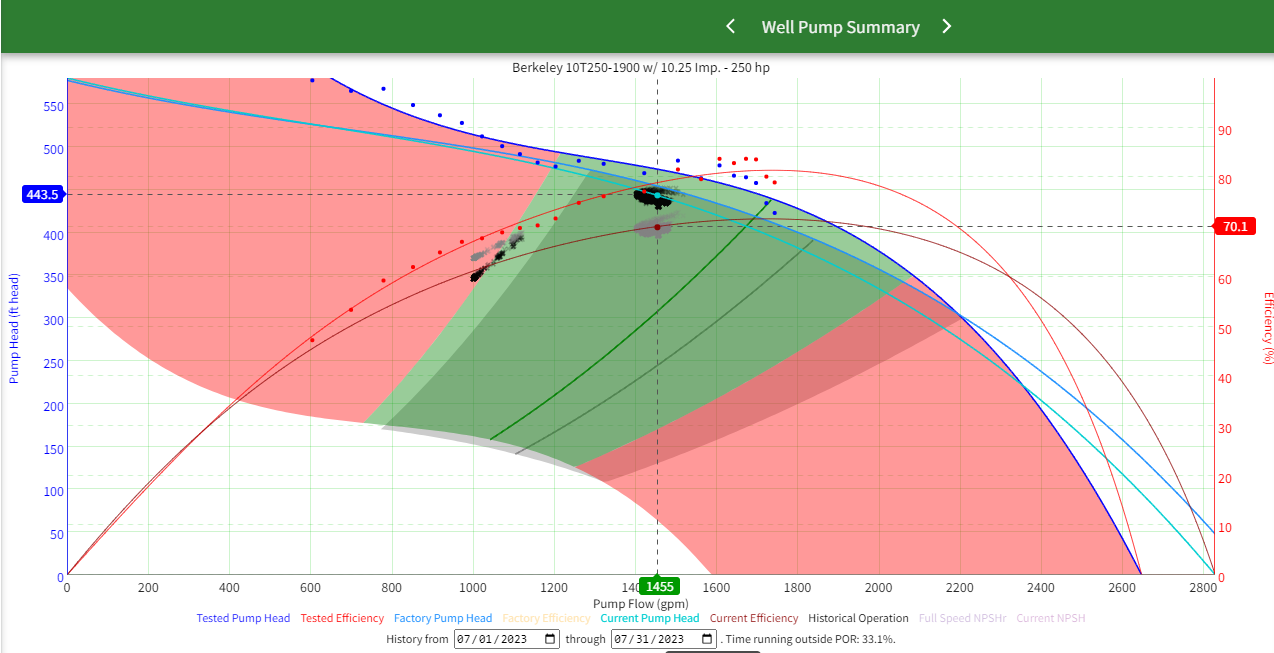
With optimization, Aqua staff recognized that the pump could be run longer at lower speeds, thereby increasing the expected life of the pump. The DPO also takes into account the impact of net positive suction head (NPSH) on the performance of a pump. While most industry well pumps are operated to 100% then ramped down to meet flow (or many times just operated to single setpoint), the DPO makes active advisements based on the NPSH available due to active work being performed by the aquifer level. This calculation allows the pump to operate most of the time at the left edge of POR, thereby lowering consumed power. In addition to using the aquifer to the advantage of the pump operation, the more NPSH that exists on a pump the less likely it is to cavitate, resulting in a decrease to pump maintenance needs.
The well has seen significant decreases to required maintenance. Since the DPO system was installed in 2012, the pump has run over forty-four thousand hours and pumped over 2.5 billion gallons of water without being pulled out of service once for maintenance. The real-time curves also show that the pump is operating at near factory conditions. If the pump had been run faster during this time (and not taken advantage of running at the left of POR), it most likely would have been rebuilt 3-4 times in the last 10 years.
Tracking Pump Health Index
All pumps wear over time. Knowing when to schedule repairs or replacement is critical to maintaining pump efficiency and capacity. Specific Energy’s DPO gives operators the ability to initiate an automated pump test that will compute the Pump Health Index (PHI). By tracking PHI of pumps across their water system, Aqua’s operations staff can preemptively schedule pump asset maintenance before pumps become excessively inefficient.
Monitoring the Aquifer
Collecting data and computing well metrics is key to monitoring an aquifer’s condition. The DPO collects well pumping levels and acquires well recovery curves to extrapolate static aquifer levels. Well S8’s specific capacity is recomputed and permanently logged after each pump run. These aquifer metrics give operators and engineers greater insight into aquifer conditions over time.
Well Production Increase
As mentioned above, Aqua’s desire was to increase production from this well cost-effectively. Due to the knowledge provided by the DPO operation, Aqua’s engineering firm was able to recommend replacement of portions of the column, a new motor, and a new VFD. From these changes alone, combined with the DPO operation using maximized NPSH at the left edge of POR, Aqua was able to experience a new maximum flow of 1,800 gpm (an increase of 700 gpm over the original design flow). This project was completed at a very economical cost of $150,000, compared to a new well cost of over $2,000,000. Aqua was very pleased with this wise use of their funds.
Summary
Due to the use of DPO, Aqua now benefits from the following strategies which are not commonly seen in well field pumps.
- Aqua can confidently operate at the lowest speed/energy usage to keep pump within POR and meet demand
- Aqua can run the pump with NPSH maximized, thereby operating at the lowest specific energy and significantly increasing the life of the pump.
- Aqua has a dashboard that lets them know where the pump is operating on its curve and allows intelligent data gathering and infrastructure planning.
- Aqua doesn't have to run the pump at constant or predetermined levels, but instead operates at the best points possible using dynamically changing, real-time information.
- Aqua can dispense with the deration of their wells at design, being able to rely on active tracking.
- Aqua can now track the historical performance of their aquifer and its impact on pump operation.
- Aqua can now operate and view their pump in such a way as to have confidence in the health of their infrastructure.